Design, installation, balancing, testing and maintenance of air conditioning systems
HVAC systems are Heating, Ventilation and Air Conditioning systems that are necessary for comfort and for guaranteeing the environmental conditions necessary for specific productions.
HVAC systems often consist of several components including valves, pumps, fans, compressors, air handling units (AHUs) and fan coil units (FCUs) each having individual performance characteristic curves. Ensuring optimal performances of HVAC systems over a broad spectrum of operating loads imposes specific component customization and sizing challenges.
Tecno Electric has gained experience and expertise over the years in design, installation, balancing and maintenance of HVAC systems that are capable of satisfying every need.
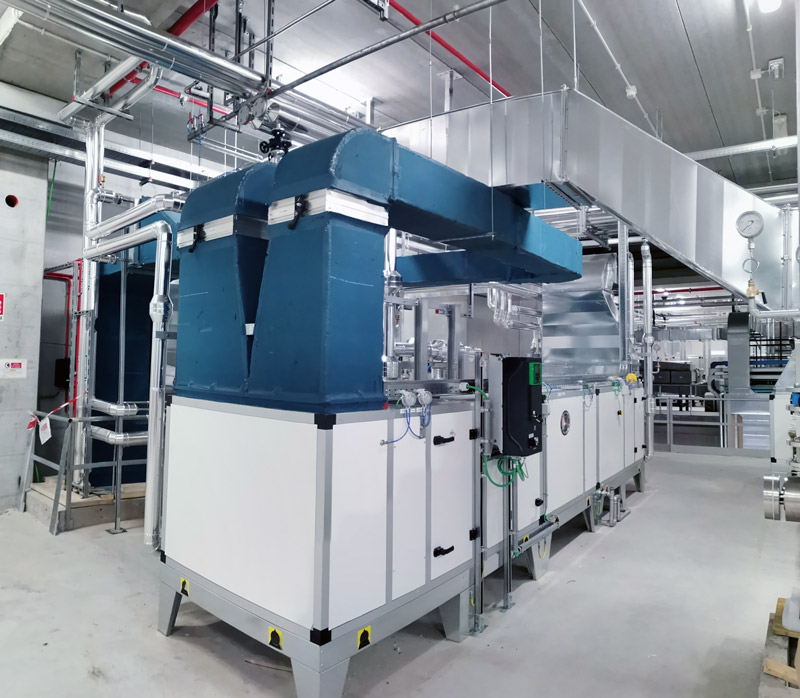
IMPIANTI HVAC
DESIGN
HVAC systems design includes:
– definition of air flows, environmental classes and overpressures;
– preparation of P&IDs, duct plans (single-line, 2D and 3D), terminal element plans;
– AHU and post coil zoning;
– Analysis of pressure flow trend;
– duct sizing;
– sizing of AHU, coils, regulation valves , terminal elements;
– determination of required instrumentation;
– definition of thermal loads and necessary utilities;
– preparation of operating logics and technical specifications;
– development of estimates of bills of quantities and determination of the investment budget;
– development of activities time schedule.
IMPIANTI HVAC
INSTALLATION
Installation of air conditioning systems complete with ducts, insulation, coils, regulating valve groups, air filtration systems for Pharmaceutical, Research, Service industries environments.
Installation of air conditioning systems for offices, electrical substations, UPS rooms, CED (Split, VRV, precision machines).
Definition and installation of instrumentation and control system for the management of machines and plants, the regulation of the flow rate and of the ambient parameters (pressure, temperature and humidity).
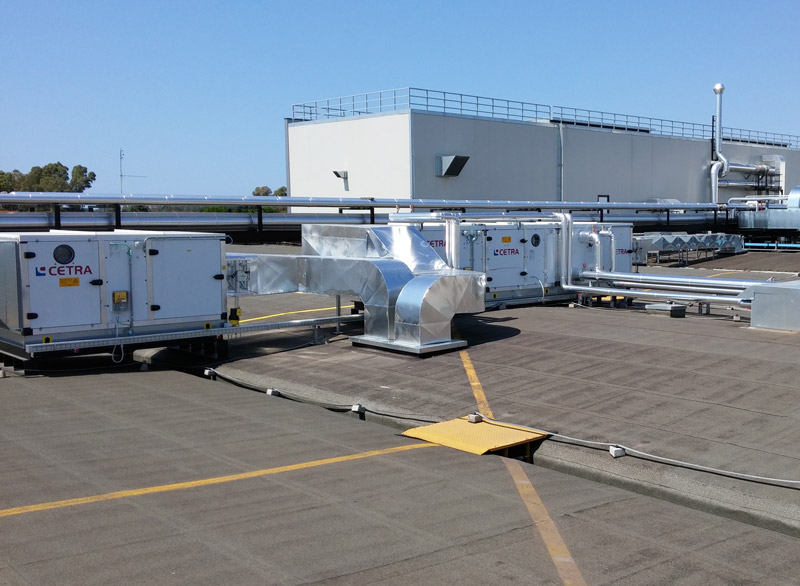
BALANCING
– Measurement and balancing of the air flows on the aeraulic components, in the conveying channels and in the air treatment units.
– System commissioning;
– Validation of machines and systems for checking their optimal functioning after installation (SAT-IQ-OQ).
– Duct seal test according to UNI EN 1507 and UNI EN 12237.
– Verification of environmental parameters in classified environments.
– Integrity testing of high efficiency HEPA filters.
– Verification of the cleanliness of the air inside classified environments.
– Training of maintenance personnel on the correct use of the systems.
– Extensive investigation of existing systems to ensure that all components operate properly.
– Balancing of systems to meet effective demand and to optimize operating costs.
SYSTEM MAINTENANCE
– Filter replacement.
– Batteries cleaning.
– Bearing replacement, pulley alignment.
– Washing and sanitizing of U.T.A, splits, fan coils and aeraulic ducts.
– Electrical, mechanical and instrumental checks.
– Calibration and certification of control instruments.